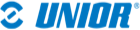
Vous pourriez avoir besoin de
Integral drum brake
A rear brake with an integral hub and brake drum. The riveted lining on the leading (rear) shoe is positioned off centre in the direction of wheel rotation.
Check drum brakes at least every six months, 6,000 miles or 10,000 km, or as recommended in the car's normal service schedule. Look for worn brake linings.
Later cars often have a plugged inspection hole in the backplate. On other cars you need to remove the drum.
Linings may be riveted or bonded to the brake shoes. With riveted linings, replace the shoes well before the lining wears down to the level of the rivet heads. Exposed heads score and ruin the brake drums.
This video course is the best way to learn everything about cars.
Three hours of instruction available right now, and many more hours in production.
- 4K HD with full subtitles
- Complete disassembly of a sports car
Separate drum brake
A front brake with a drum separate from the hub. The hub stays in place when the linings are changed.
Shoes with bonded lining should, for safety, be replaced when the lining is worn to & 1/10 in. (3 mm) thick, even if a minimum thickness of 1/16 in. (1.5 mm) is quoted in the car handbook.
Always renew brake shoes on both wheels on an axle, even if the lining on one wheel is less worn than on the other. Renew on both wheels also if one lining has been fouled by oil or brake fluid. Otherwise, braking will be unbalanced.
Buy only brake shoes that have a well-known maker's name clearly marked and correctly spelled on the box. Dangerous fakes are common they often have names only slightly altered from a well-known make.
If you have to get under the car, to look through the inspection hole in the backplate, for example, raise the car and support it on axle stands, not just on jacks.
When working on brakes, take care not to inhale brake dust from drums it contains poisonous asbestos, used in the manufacture of the linings.
Work on rear brakes has to be done with the handbrake off - be sure to chock the wheels on the ground firmly on both sides.
When dismantling brakes, have a pencil and paper ready to draw the sometimes complicated way in which certain parts fit together.
Vital details include which way round brake shoes fit; the holes into which springs fit (there may be several similar-looking holes near the correct one); which way round springs go (the ends are often not the same length); the position of retaining pins and automatic adjustment parts; and the order in which washers are fitted.
If the brakes are adjusted manually, slacken them (See Adjusting the brakes) before you remove the drums. With self-adjusting brakes, slackening is usually neither necessary nor possible.
A few cars have a hole in the drum through which you can use two screwdrivers to lift the pawl off the adjusting ratchet wheel and turn the wheel back.
The brake drum may be integral with the wheel hub, or separate.
Removing an integral drum
Prise off the central cap with a screwdriver, working evenly around its lip.
Prise off the central cap with a screwdriver if you can; lever evenly round the edge — if it becomes crooked it will stick.
If levering fails, try tapping gently round the edge of the cap with a hammer and chisel.
If the cap has no lip to give you leverage, drill a hole in it, insert a self-tapping screw and pull it with a claw hammer. Plug the hole before refitting the cap.
If all else fails, knock off the cap with a hammer and chisel — new caps are inexpensive.
Prise off the central cap with a screwdriver, working evenly around its lip.
Under the cap there may be a castellated nut, or a castellated cap over a plain nut, held by a split pin. Straighten the legs of the split pin and pull it out, starting by tapping it with a hammer if necessary.
Always use a new split pin when reassembling.
Examine the nut carefully to see if it has a left-hand thread. It is tightened to a precise torque, which varies greatly from car to car. Before refitting, check the figure with your local dealer or the car service manual.
For very tight nuts, ask a helper to apply the brakes while you unscrew the nut using a length of pipe over the socket-wrench handle to give extra leverage.
With the nut removed, pull the drum off by hand if possible. It will come away complete with bearings. Spread a cloth on the ground to catch any bearings that may fall.
With the nut removed, you may be able to pull the drum and hub off by hand. Spread a clean rag on the ground — sometimes a bearing falls free as the hub comes off.
If the assembly is stiff, try refitting the wheel and pulling that. But do not lever the lip of the drum, or you may damage it. In severe cases you may need a hub puller , which you can hire if necessary.
You may also need a hub puller if the inner track of the inner wheel bearing stays fixed on the axle, as it sometimes does. Put a hose clip round or behind it to give the puller legs a good grip.
Removing a separate drum
Remove the bolts or screws securing the drum. Tap stubborn set-screws with a centre punch, offset from the slot, in the unscrewing direction. Or use an impact driver.
The drum may be held on by one or two set-screws or hexagonal-headed bolts. Remove them.
Alternatively, the drum may be held by a spring clip on one wheel stud, or there may be no fixing at all.
Once the stubborn set screw is loosened, finish unscrewing with a screwdriver.
So that you can refit the drum in the same position, paint a mark on one wheel stud and against the hole in the drum through which it fits.
If the wheel has been balanced on the car, the balance of the brake drum will have been taken into account. Refitting it in the same position will avoid upsetting it.
Mark one wheel stud and hole with paint so that you can refit the drum in the same position.
Pull the drum straight off if you can. If it sticks, try tapping all round the edge of the drum — not the lip with a soft-faced hammer.
Do not try to lever the lip away from the backplate — you may damage it.
If the drum sticks, tap round the edge with a soft-faced hammer. Take care not to hit the lip of the drum or the backplate.
If tapping fails to move the drum, put penetrating oil on the studs and the joint between the drum and hub, and leave it for a while. Do not get oil in the drum.
Another method is to wrap the drum in rags and pour boiling water over it to make the drum expand.
Removing brake shoes
Remove a coil hold-down spring by holding the pin from the rear and pushing and turning the cap with pliers until the pin end lines with the cap slot.
To take off any type of brake shoe, the hold-down springs and sometimes the pull-off springs have to be removed. The procedure for removing twin leading shoes varies slightly from that for removing leading-and-trailing shoes.
Make detailed notes and drawings, or take photographs, of all parts before you remove anything.
Generally, refitting is in the reverse order of dismantling.
A capped coil spring may secure the pin holding the brake shoe to the backplate.
The shoe hold-down springs may be either small coil springs or spring clips.
They fit over pins, one on each shoe, that pass through the backplate and the shoe.
Each coil spring fits under a small dished cap with a slot in it. The end of the pin is flattened and fits through the slot in the cap and lies at right-angles to it.
To remove, grip the cap with pliers and push it down while you hold the pin from the rear of the backplate.
Turn the cap until the flattened pin end aligns with the slot. Pull the cap off. To remove a spring clip, press it down with pliers until you can pull its forked end clear of the flattened head of the pin.
Removing a spring clip
Remove a spring clip by pressing it down with pliers until the forked end can be pulled clear of the pin head. The forked end of the clip secures the T-shaped pin holding the brake shoe to the backplate.
Removing pull-off springs
If you have to remove pull-off springs, use a strong hook and force it into the web hole to grip the spring.
On most cars you do not need to remove the pull-off springs before taking off the shoes. The shoes with springs attached can be lifted over the hub as a pair. But on a few types of car the hub is rather wide and covers the springs, so they have to be unfastened.
Pull them off with a strong hook. You can make one by driving a 4 in. (100 mm) nail sideways through a length of broom handle and bending the point.
Use a screwdriver braced against a bolt on the backplate to lever the shoe free from the slot in the cylinder. Then lever the shoe away from the backplate.
If necessary, use pliers and a screwdriver to force the hook inside the hole in the shoe web, in the right place to grip the spring.
There may be a cut-out in the hub edge that you can turn in line to make it easier to reach into the hole.
The springs hold the shoes so that the ends fit into slots in the cylinder, and the shoes must be freed from the slots before you pull them off.
For freeing the shoes there is a special tool called a shoe horn, but if you do not have one you can lever them away from the cylinder with a screwdriver braced against a bolt on the backplate. Or use pliers or a self-locking wrench.
Removing the shoe and securing the cylinder
On brakes with twin leading shoes, remove the hold-down springs and then unhook each pull-off spring to take off each shoe separately.
Once the shoe is clear of its retaining slot, pull it off towards you.
On brakes with twin leading shoes, remove each shoe in turn, detaching its spring.
Leading-and-trailing shoes have a spring stretched between them. If you lever the trailing shoe out of the cylinder, you can usually remove both shoes at once.
To remove the pull-off spring, you may first have to ease the pressure on the spring by releasing the shoe from its wheel-cylinder mounting.
The leading shoe of a rear brake is slotted over the handbrake lever, and there is often a support plate in the slot. Keep this plate for fitting to the new shoe.
As soon as the brake shoes are off, put string or strong rubber bands securely round the wheel cylinders to stop the pistons falling out.
Be very careful not to get oil on the linings of the new shoes. If necessary, protect them with adhesive tape while you are fitting them. Remember to peel it away before replacing the drum.
Tips for reassembling brake shoes and drums
Using a brake shoe horn
A tool known as a shoe horn frees the shoe more easily.
-
Clean brake dust from the linings and the drums before refitting. It often causes brake squeal.
Take care - asbestos used in the manufacture of brake linings is extremely poisonous, and is present in the dust Use a vacuum cleaner to remove it if possible.
- Make sure that any brake or handbrake adjustment mechanisms are retracted and will not be in the way when you refit the drums to the wheels.
- Make sure the shoes are central, or the drum will not fit. Hold the drum against the shoe assembly and adjust the shoes slightly until you can slip the drum over them easily.
- After fitting the drums, and before you adjust the brakes , press the brake pedal a few times to centralise the brake shoes within the drum.